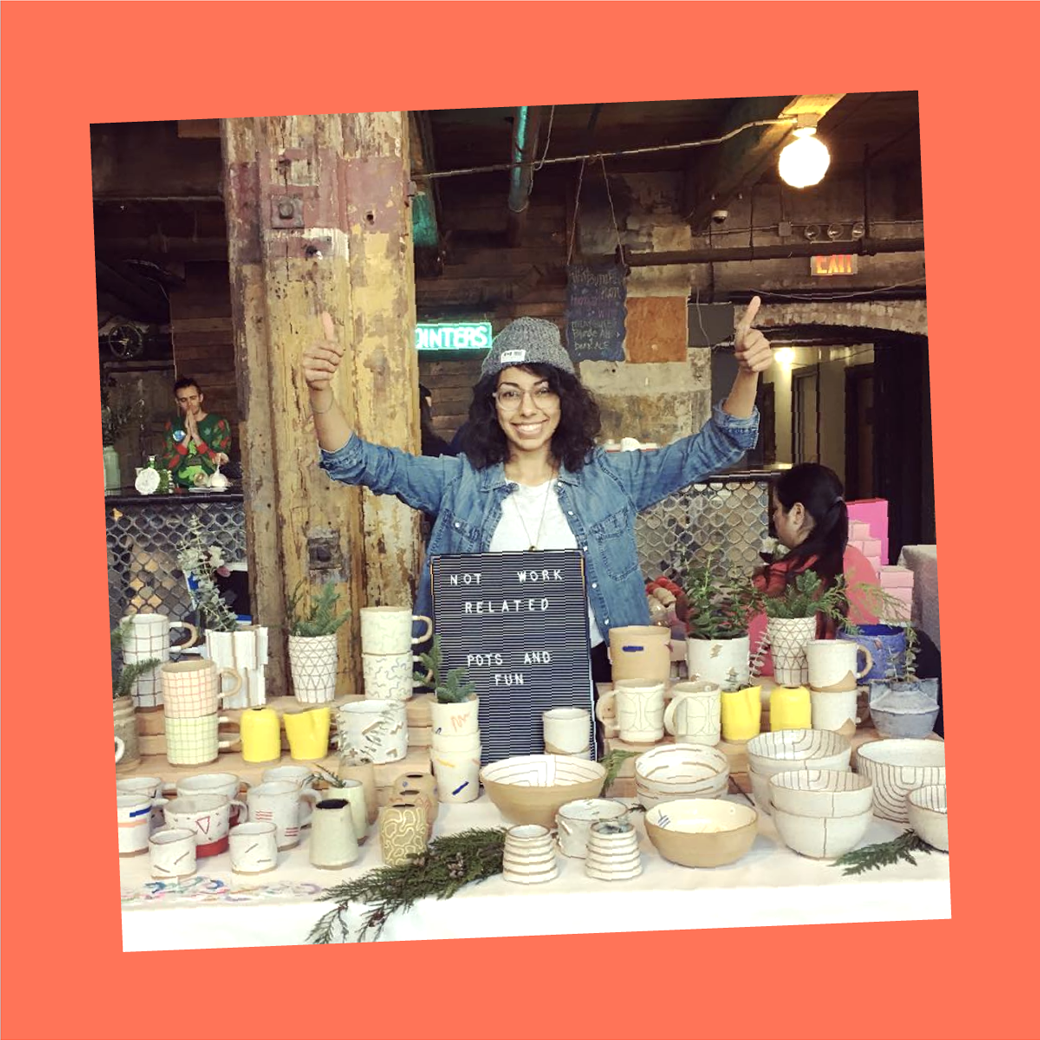
Below, Sarah tells us about the love that went into designing these bowls, from the unique dachshund-themed shapes to the development of a new production technique to bring these bowls to life. Read on to get to know Sarah and get a peek at some of the behind-the-scenes magic.
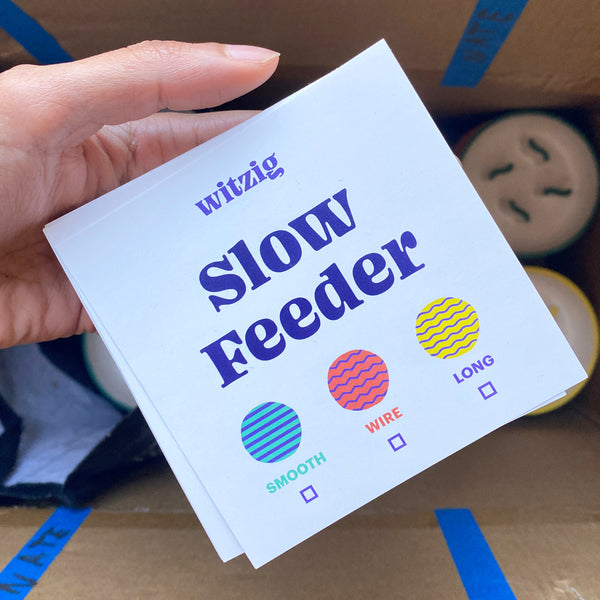
Have you always made ceramics?
I went to school for architecture, and got my master's from Columbia. When I started working full time at an architecture firm, I got really restless, because I had never sat still for so long. I missed the physical experience of building things, and so I started doing ceramics on the side. I had done ceramics in high school and gravitated towards the medium. As I was getting started, I made primarily everyday objects like cups and vases, which were the most familiar to me. Eventually though, as I grew in confidence, I expanded into planters and mugs, which are my staples today, and began adding attachments and holes to my designs.
In 2017, the architecture firm where I was working was very large. It was the kind of place where you’d get in in the morning and not know when you were going to leave, or if you were going to be working through the weekend. It was a pretty brutal, soulless experience. During that time, I started selling my bowls, mugs, and planters at local markets, and I was surprised by how much people were buying. I decided to quit my job, and found a freelance job that I could do on the side while I was shifting more towards my ceramics.
It’s taken about three years to transition from a career in architecture to what I’m doing now, but my architecture background still plays a role in my work — especially in the 3D modeling and all the illustrations that I make when I’m conceiving or proposing a project. These tools help me design and visualize a product before producing prototypes and samples, and also make it easier for me to communicate my design intent to clients. I hope that bringing these skill sets together challenges what I’m able to produce.
Do you have a favorite type of project to work on?
I love things that are repetitious. There’s something about making the same thing over and over again allows for efficiencies that you just don't encounter when you're making one-offs. My dream project is probably making 100 of the same thing. Most people would hate that, because it’s monotonous. But it's actually really wonderful to be able to turn your brain off a bit and allow the muscle memory to take over. It's a pretty special physical experience.
What did you learn about dachshunds when you were designing the bowls?
I had never heard of slow feeders, and when I first learned about the need for them, I thought there was something adorably hilarious about it — that these tiny dogs get so excited about their food that they eat too fast and need a physical distraction to slow them down.
It also took me a little bit to figure out the right size for the bowls. The prototype I brought to Witzig’s New York event was huge, because for some reason it hadn’t hit me how small dachshunds are. I’m most familiar with border collies, and I think I had originally made the prototype with that size dog in the back of my mind. Once you see dachshunds in real life, though, you realize how tiny they are. The bowl was basically as big as they were! After talking with a lot of dachshund owners, I realized I had to really shrink it down, and the final product ended up being half as tall.
When you started thinking about the slow feeders, how did you incorporate the spirit of dachshunds into the design?
During the brand development stage, the Witzig team had come up with the idea that different line types would represent different types of dachshunds. There was a straight line (for smooth coats), a squiggle line (for long), and a zig zag line (for wire). I thought that was a super interesting way to incorporate the brand’s focus on what makes dachshunds special into the bowls and make the product feel very Witzig, as though the identity was part of the product.
Creating these dachshund-themed shapes not only was on-brand for Witzig, but also had a strong connection to the Not Work Related pieces that I produce all the time. I make a lot of mugs and planters that have shapes on the outside, so it felt very natural to take something that I would typically do on the outside of the piece and move it to the inside. It was an inverse of something I have been doing for a long time. The three-dimensionality of the shapes was something that married the two.
Did you encounter any challenges when you were designing the bowls?
Because the shapes inside the slow feeder bowls are much taller than the shapes I make for my ceramics, I couldn’t use 3D printed stencils like I normally would. I ended up using an extruder instead, which is a type of manual machine that I typically use to make handles for my mugs.
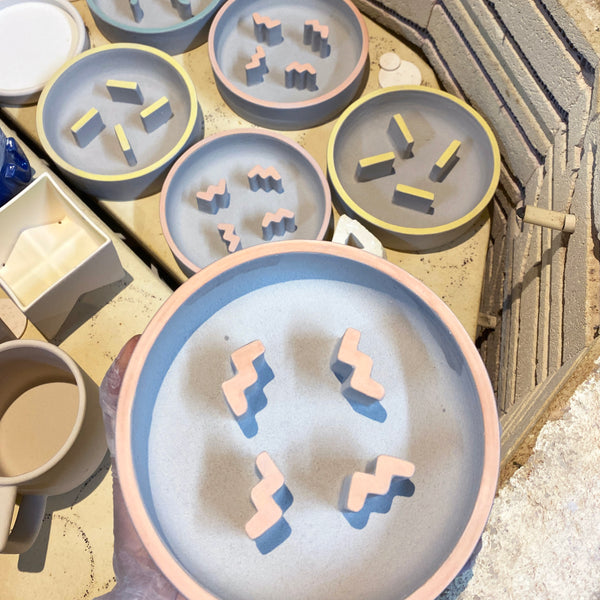
For the slow-feeders, though, I modeled a die that would give me the shapes I needed, and my friend 3D printed for me. Instead of a tube coming out the end of it that’s the size of a mug handle, I got a tube that was the shape of a zig zag or a squiggle. Figuring that out was a huge breakthrough for me in producing the dog bowls. Once I had the shapes, I let them set and then chopped them up. They could be as tall as I wanted, and it was all very consistent.
What is the process like for you to make the bowls?
First, the bowl is thrown on the wheel, and then it’s trimmed, meaning the bottom of the bowl is cleaned up so that everything is even. This is also when I make the foot ring, which is the little ring at the bottom that keeps the bowl from being completely flat to the surface.
Next, I attach the line shapes to the inside of the bowl. I use a method called “scratch and attach” to secure the pieces of clay together — it’s very similar to the way I attach shapes to my mugs and planters.
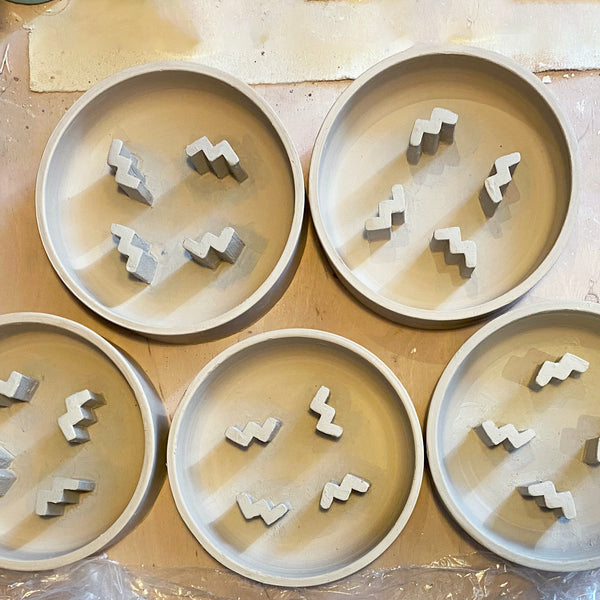
Finally, I paint the color on the bowls before I fire them. Because the color is just on the top of the shapes, it’s very hard to just paint the edges, so using wet clay means that I can sponge away any paint that bleeds over the sides. This makes the appearance much cleaner than if I waited until after the bowls had been fired in the kiln.
Do you have a favorite of the three slow feeder bowls?
I love the smooth (yellow) design. It was the first one I prototyped and I’m especially fond of it. I'm also partial to yellow, so I'm playing favorites.
Are you a dog person?
Yeah, definitely. I’m a dog person over a cat person for sure.